I ran into a big problem when trying to install the CURT 31087 front hitch. I was tightening the M14 Hex bolt (red in the picture) provided by CURT to the weld nut(blue in the picture), using the torque wrench, and set it to 88 lb. It is very tight so I forced it in then the weld nut just came off. The frame is boxed and no easy way for me to access the loose bolt and nut. It just hanged in the middle of the frame. See the picture for detail. Any idea how to access the inside of the frame (hollow)?
Also, I attached the picture of the bolt for the driver's side. I am curious if Ram has changed the size of the nut and if I am using the correct bolt (M14, according to CURT).
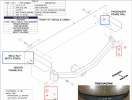
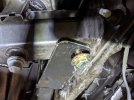
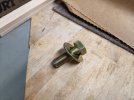
Also, I attached the picture of the bolt for the driver's side. I am curious if Ram has changed the size of the nut and if I am using the correct bolt (M14, according to CURT).
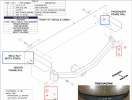
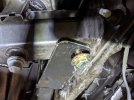
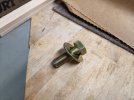