Granite2WD
Well-Known Member
- Joined
- Dec 8, 2019
- Messages
- 218
- Reaction score
- 148
- Points
- 43
- Age
- 35
Why is its coil spring rear suspension such a big deal? Dan Edmunds explains why
www.autoblog.com
What is taking everyone so long? That’s what I continually ask myself each time yet another all-new full-size pickup comes out with leaf spring rear suspension. Meanwhile, this 2020 Ram 1500 pickup represents a dozen years since coil spring rear suspension debuted when its prior generation was still being called a Dodge Ram 1500. Ford, Chevrolet, Toyota and Nissan introduced full redesigns of their pickups well after Ram proved that coil springs were the way to go, and yet leaf springs persist with the competition.
I’m not just popping off, here. In the 1990s I used to specialize in pickup truck suspension tuning for the Toyota Technical Center. Leaf springs are crude and loaded with compromises, but that’s all that truck design engineers ever gave us to work with. I was instantly all-in on Ram’s move to rear coils after the first few miles of driving a 2009 Ram 1500 pickup. Empty-bed ride comfort and handling were on another level, but it could still tow and haul. In fact, towing stability proved to be frankly incredible on the normally-treacherous downhill leg of my winding tow test grade. I fully expected everyone would copy it immediately.
But they didn’t. Others may have doubted the payload aspects. Ram never did. It soon doubled down and put coils under the back of its 2014 2500-series trucks. I’ve developed other theories that seek to explain why no one followed their lead, but they’re not worth dredging up because I think the dominoes will soon begin to fall. Spy photos suggest that the next Toyota Tundra will switch to coils, and there are rumors that the Ford Raptor is going that way. That’s not much of a stretch because the Ranger Raptor (only available outside the U.S.) already has coil spring rear suspension.
What’s the big deal? Let’s take a look at the underside of a 2020 Ram 1500 Laramie 4x4, the second iteration of the Ram 1500 to employ coil spring rear suspension.
As it has for some time, the front end of the Ram 1500 rides on double wishbone suspension. The truck employs a high-mount upper wishbone (yellow arrow) that positions the upper ball joint up behind the tire sidewall instead of inside the wheel’s barrel. This layout offers improved steering geometry and reduced stress in the upper ball joint, the upper control arm and its mounting points.
Coil-over spring/shock assemblies (green) come standard on all 2019+ (fifth-generation) Ram 1500 pickups whether they have four-wheel drive or not. But the presence of coil spring rear suspension has bearing even up here because it allows Ram to offer four-corner air suspension as an option.
If that option were present we’d see a cylindrical air spring enveloping the front shock instead of coil spring. The small ball on the upper control arm (yellow) would be connected to a linkage feeding into a suspension position sensor to help the system manage the vehicle’s ride height.
The lower wishbone (yellow) and steering knuckle (red) were made of aluminum in the prior generation, but further weight reduction and design optimization steps have been taken. That’s most obvious when looking at the lower wishbone, which no longer has an extra flange on this side for the front stabilizer bar linkage. Camber and caster adjustments are made with a pair of eccentrics (green) at the wishbone’s mounting points.
The upper control arm is quite broad, and the coil-over shock is not centered between its arms. The reason for this seems to be that the shock’s lower mount is positioned next to the front drive axle, and the shock body is at full width at the point. If you’re not with me, don’t worry. We’ll see more of this later. Besides, the breadth of this wishbone is not its most interesting aspect.
That upper wishbone is a highly-engineered piece made up of two parts that are bonded together. The upper surface is a thin but deeply-drawn steel stamping (yellow) that is welded to otherwise-normal cylindrical steel bosses that house its pivot bushings. This creates a deep u-shaped steel shell, within which they have bonded a molded composite structure (green). The end result is an upper arm that is considerably lighter than it would be otherwise.
Weight reduction isn’t the only benefit of this construction. This arrangement undoubtedly transmits fewer road vibrations in through the chassis and on to the cabin.
This photo may explain why the upper wishbone is so broad. The shock absorber maintains its full diameter (yellow) all the way to its mounting point. The piston within can use most of the visible length. This obviously makes the lower end of the damper fatter, but that in turn means it must reside farther forward (left in this view) to stay clear of the drive axle.
If this was a Toyota we’d see a slender rod in this area, with the shock’s working diameter ending above this point. That allows their shocks to hug closer to the axle, but such shocks must extend higher at the top to maintain sufficient suspension travel. This may explain why the Ram’s high-mount upper arm pivot (and the upper shock mount that’s usually part of that structure) isn’t positioned nearly as high as we’d see on a Toyota.
The 2019+ Ram 1500’s stabilizer bar (yellow) has been moved from its former position ahead of the axle to this position behind the axle. It’s a very tidy installation. They say it results in a 20% increase in roll stiffness, but the old installation seemed to have room enough for fatter bars that could offer that kind of gain.
I think the real reason for the increased roll stiffness has to do with the capacity of the linkage mounting point (green) on the lower wishbone. The old design’s mounting point was a flange that protruded away from the main wishbone casting. They were probably near the limit of what it could take. Whether that’s strictly the case or not, this design transmits the stabilizer bar load into the very meaty central part of the wishbone. I like how it mirrors and counterbalances what’s going on with the shock, too. All of this results in a tidier and lighter lower wishbone design.
The distortion in photos like this always make estimating motion ratios a little dicey, but I’m going to plow ahead anyway. The point isn’t to reverse engineer this truck, just see what it's all about.
Looking first at the inner pivot at the frame and the outer ball joint at the steering knuckle, our spring shock assembly bolts to the arm about 75% of the way out. Every inch of suspension travel will result in 0.75 inch of spring and shock movement. The stabilizer bar link looks like it lines right up with that, but you’ve got to follow the mounting bolt down from the flexible joint hidden inside that rubber bellows. That reveals a motion ratio of about 60%, or 0.6 inch of stabilizer bar linkage movement for every inch of wheel travel.
Many trucks have mechanical steering stops, and the Ram 1500 is no exception. The lower wishbone has a special protrusion that matches up to a zone built into the steering knuckle. This one comes into play at full left lock, while a similar setup on the passenger side does the job at full right lock. This doesn’t happen often, and there’s never pressure for extended periods, so it's fine. I prefer this to having the steering gear itself hit a hard internal limit.
Normally we only see the bumps in the casting that give away a caliper’s pistons, but here we can see where this sliding caliper’s two pistons press against the inner brake pad. But it's not just the inner pad that does the work. The caliper itself slides (hence the name sliding caliper) on two pins as force is applied so that half of the clamping force generated by the inner pistons passes through the structure to the pads that are arrayed on the opposite side of the rotor.
It’s like grasping something between your fingertips and palm. Your fingers appear to be doing all of the work, but the item you’ve grabbed is experiencing the same clamping force on both sides.
Just about everything we’re seeing at the back of the Ram 1500 is unique in the North American pickup world. The only truck that’s similar is the new Jeep Gladiator, which makes sense because that truck only exists because it had this truck to borrow from.
This rear suspension type may be unique among pickups, but this layout replaced leaf springs underneath frame-based SUVs more than three decades ago. People ride in the back of those, not bags of cement, so the ride and handling benefits were recognized as essential long ago. In fact, full-size SUVs have even moved on from there to the next level: independent rear suspension. And then there are all of those crossovers of all sizes.
Full-size trucks that tow and haul may not ever go that far, but this layout does make a lot of sense — especially since most trucks nowadays are sold with humongous crew cabs and shorter 5.5-foot beds.
Ram calls this link-coil suspension, but its other names include five-link rear suspension and four-link rear suspension. Those mean the same thing, with the difference coming down to a friendly disagreement on the status of the panhard bar, which both of them have.
Here we can see two trailing links (yellow), and you can imagine the two just like them on the other side. Atop the axle sits the all-important coil spring (green). The shock absorbers (red) can lean forward on both sides here because the four trailing links control axle windup. There’s no need for the staggered shock arrangement that leaf-spring trucks must use.
Unlike leaf springs, coil springs only have one job. They’re also better suited to that job because there are no sliding surfaces that come into play as they compress. The 2019+ Ram 1500 has progressive rear springs, which is why the coils appear closer together at the top. This allows the initial movement to be softer in the unladen condition, then tighten up as the suspension compresses over bigger bumps and when the truck is burdened with a load.
It’s easy to imagine how an air spring can be substituted very easily. Everything else pretty much stays the same. A height sensor would be connected to the nub (yellow) on the uppermost trailing link, and there would be a few valves and hoses that run off to an added air compressor.
One of the many advantages of link-coil suspension is a reduction in weight. When it first came out in 2009 Ram claimed a 40-pound weight savings, with much of that being unsprung weight. Leaf springs are long, thick and heavy. These links are something like a third as long, and they’re hollow. As for the coil springs, they don’t weigh much.
Here is link number five, the panhard bar. Some will call it a track bar. Pick your poison. This is the link that keeps the axle from moving side-to-side, and it is the very presence of this link that made me so impressed with the downhill, winding road towing stability offered by this layout. Leaf-sprung trucks don’t (and can’t) have one of these. They instead depend on the lateral stiffness of the pivot bushings that live way out at their ends. That plan isn’t near as reliable as this.
The left end bolts to bracketry (yellow) that’s part of the axle, while the right end attaches to brackets (green) that descend from a frame crossmember. The axle is well braced whether you’re cornering left or right. It is as long as it is to reduce the amount of left-right translation that will occur as the suspension moves up and down.
Meanwhile, just below is the stabilizer bar (red), a feature we almost never see on leaf-spring trucks because it becomes a packaging and assembly nightmare.
The rear stabilizer bar link (yellow) attaches to a bracket on the frame.
There’s nothing too special about the upper shock mounts (yellow) other than they’re fairly conventional and easy to get at if you ever want to make a change.
Urethane bump stops (yellow) are positioned adjacent to the coil springs. The availability of optional air suspension makes it impossible to position them within the coils. Meanwhile, the rear axle is equipped with a breather tube (green) to aid water crossings.
The rear brakes on this Laramie consist of single-piston sliding calipers, ventilated rotors and an electronically-applied parking brake (yellow) that is built into the calipers.
This Laramie test truck is equipped with optional Night Package and blacked-out 22-inch rims that are wrapped with 285/45R22 Goodyear Eagle Touring tires. I didn’t expect something with this much tire width and wheel diameter (and so little sidewall) to be light, and they’re not. How does 83.5 pounds grab you? They certainly look good, though.
I drove this 2020 Ram 1500 4x4 extensively again this week, and I’m still greatly impressed with the ride this truck produces despite these heavy optional rims. And we’re not even riding on air suspension at this point. The competition has a lot of catching up to do when it comes to creating a suspension that excels at everyday use. At least one competitor seems bent on chasing payload ratings for a marketing advantage, but I think this suspension is great at keeping things real. I, for one, hope that the others get it in gear quick. That said, I’m sure Ram will be happy as clams if they don’t.
Contributing writer Dan Edmunds is a veteran automotive engineer and journalist. He worked as a vehicle development engineer for Toyota and Hyundai with an emphasis on chassis tuning, and was the director of vehicle testing at Edmunds.com (no relation) for 14 years.
You can find all of his Suspension Deep Dives here on Autoblog.

2020 Ram 1500 Suspension Deep Dive | Coil-spring rear suspension explained - Autoblog
Engineer Dan Edmunds takes a deep dive under the Ram 1500 to explain its trademark coil-spring rear suspension.

What is taking everyone so long? That’s what I continually ask myself each time yet another all-new full-size pickup comes out with leaf spring rear suspension. Meanwhile, this 2020 Ram 1500 pickup represents a dozen years since coil spring rear suspension debuted when its prior generation was still being called a Dodge Ram 1500. Ford, Chevrolet, Toyota and Nissan introduced full redesigns of their pickups well after Ram proved that coil springs were the way to go, and yet leaf springs persist with the competition.
I’m not just popping off, here. In the 1990s I used to specialize in pickup truck suspension tuning for the Toyota Technical Center. Leaf springs are crude and loaded with compromises, but that’s all that truck design engineers ever gave us to work with. I was instantly all-in on Ram’s move to rear coils after the first few miles of driving a 2009 Ram 1500 pickup. Empty-bed ride comfort and handling were on another level, but it could still tow and haul. In fact, towing stability proved to be frankly incredible on the normally-treacherous downhill leg of my winding tow test grade. I fully expected everyone would copy it immediately.
But they didn’t. Others may have doubted the payload aspects. Ram never did. It soon doubled down and put coils under the back of its 2014 2500-series trucks. I’ve developed other theories that seek to explain why no one followed their lead, but they’re not worth dredging up because I think the dominoes will soon begin to fall. Spy photos suggest that the next Toyota Tundra will switch to coils, and there are rumors that the Ford Raptor is going that way. That’s not much of a stretch because the Ranger Raptor (only available outside the U.S.) already has coil spring rear suspension.
What’s the big deal? Let’s take a look at the underside of a 2020 Ram 1500 Laramie 4x4, the second iteration of the Ram 1500 to employ coil spring rear suspension.
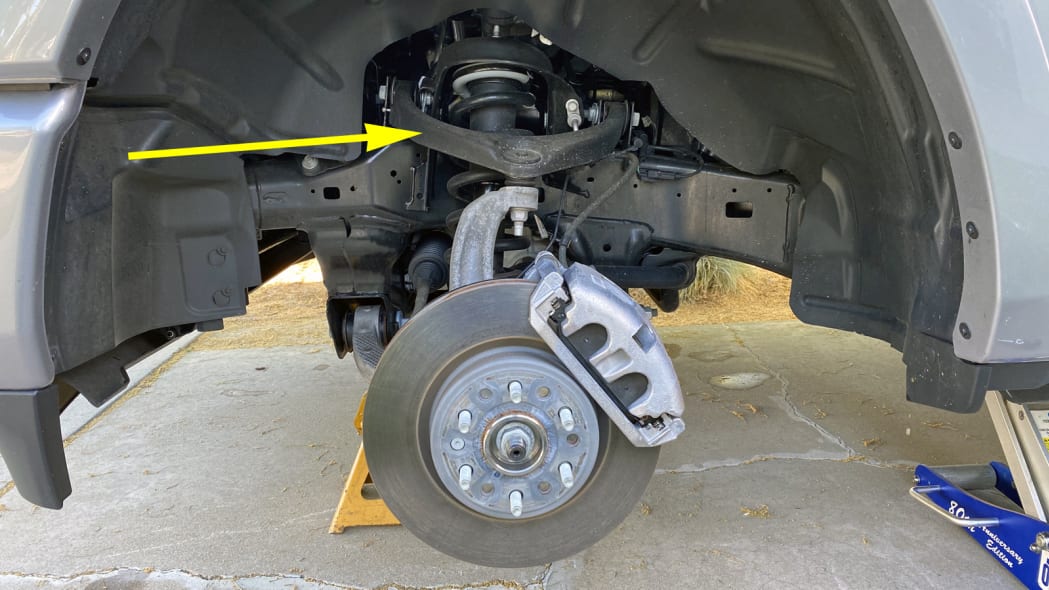
As it has for some time, the front end of the Ram 1500 rides on double wishbone suspension. The truck employs a high-mount upper wishbone (yellow arrow) that positions the upper ball joint up behind the tire sidewall instead of inside the wheel’s barrel. This layout offers improved steering geometry and reduced stress in the upper ball joint, the upper control arm and its mounting points.
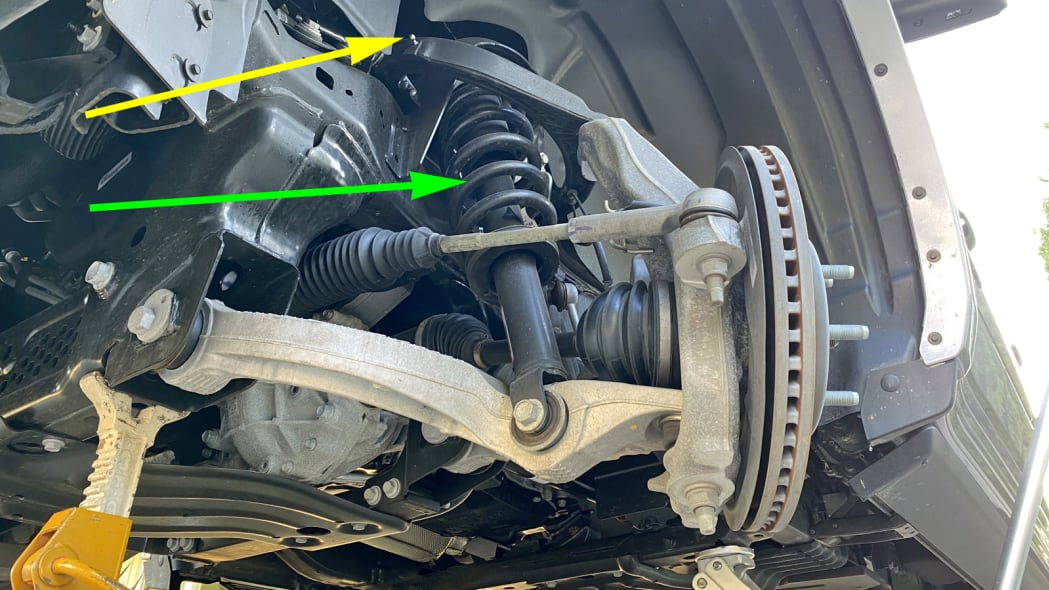
Coil-over spring/shock assemblies (green) come standard on all 2019+ (fifth-generation) Ram 1500 pickups whether they have four-wheel drive or not. But the presence of coil spring rear suspension has bearing even up here because it allows Ram to offer four-corner air suspension as an option.
If that option were present we’d see a cylindrical air spring enveloping the front shock instead of coil spring. The small ball on the upper control arm (yellow) would be connected to a linkage feeding into a suspension position sensor to help the system manage the vehicle’s ride height.
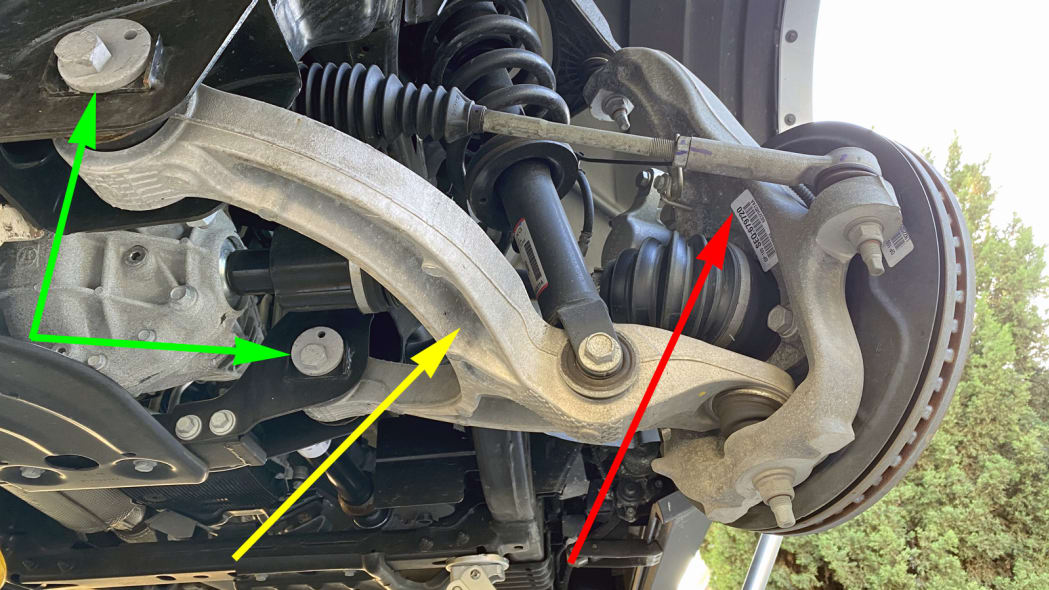
The lower wishbone (yellow) and steering knuckle (red) were made of aluminum in the prior generation, but further weight reduction and design optimization steps have been taken. That’s most obvious when looking at the lower wishbone, which no longer has an extra flange on this side for the front stabilizer bar linkage. Camber and caster adjustments are made with a pair of eccentrics (green) at the wishbone’s mounting points.
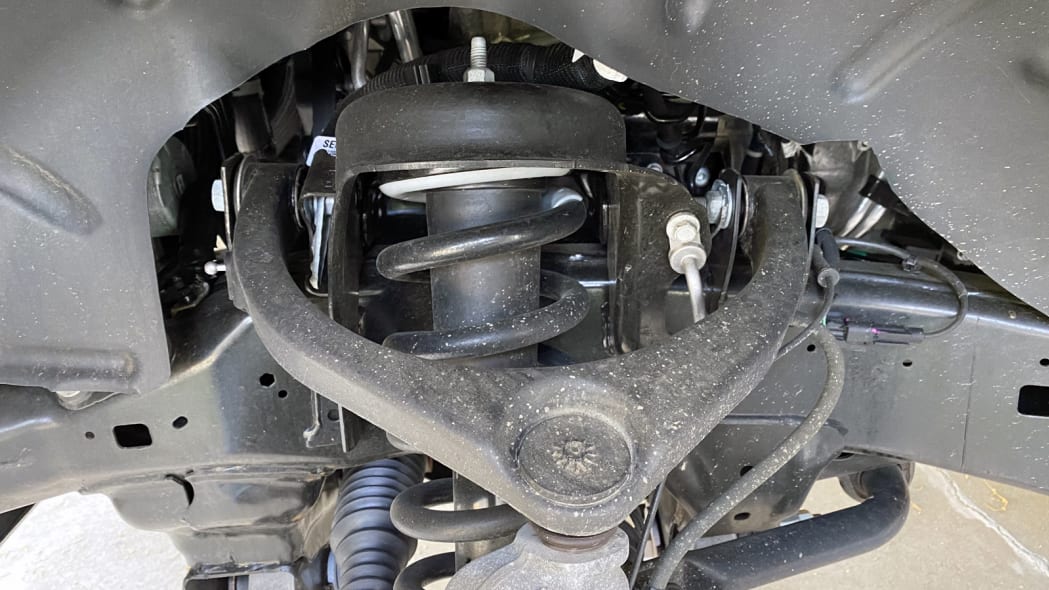
The upper control arm is quite broad, and the coil-over shock is not centered between its arms. The reason for this seems to be that the shock’s lower mount is positioned next to the front drive axle, and the shock body is at full width at the point. If you’re not with me, don’t worry. We’ll see more of this later. Besides, the breadth of this wishbone is not its most interesting aspect.
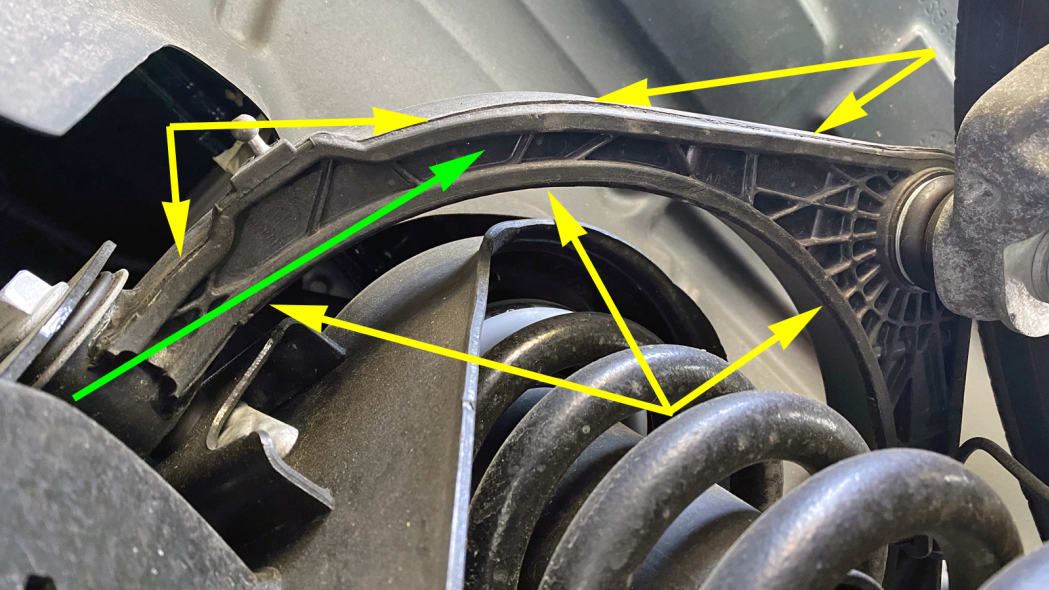
That upper wishbone is a highly-engineered piece made up of two parts that are bonded together. The upper surface is a thin but deeply-drawn steel stamping (yellow) that is welded to otherwise-normal cylindrical steel bosses that house its pivot bushings. This creates a deep u-shaped steel shell, within which they have bonded a molded composite structure (green). The end result is an upper arm that is considerably lighter than it would be otherwise.
Weight reduction isn’t the only benefit of this construction. This arrangement undoubtedly transmits fewer road vibrations in through the chassis and on to the cabin.
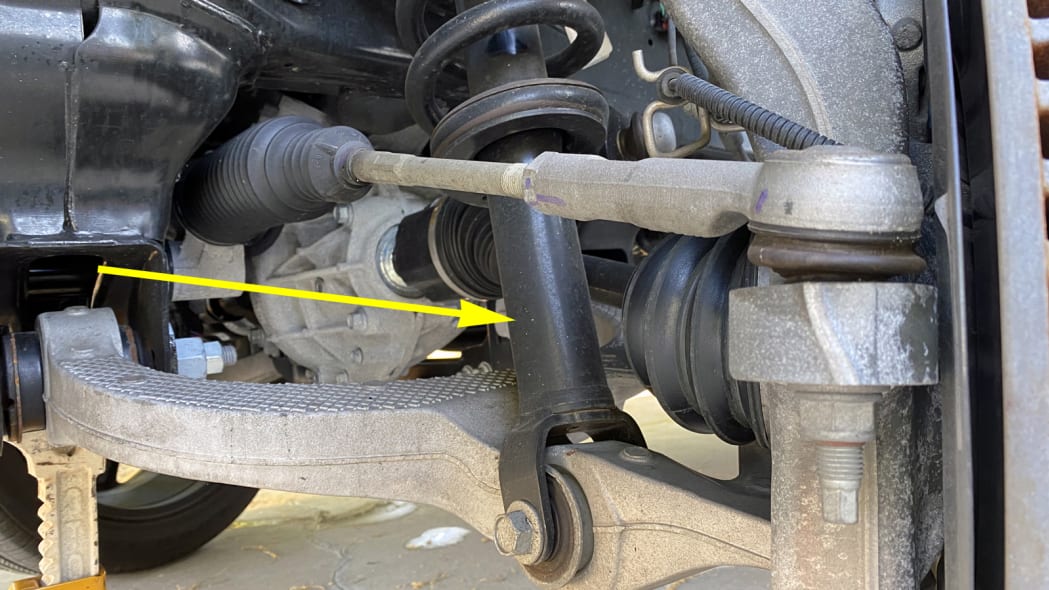
This photo may explain why the upper wishbone is so broad. The shock absorber maintains its full diameter (yellow) all the way to its mounting point. The piston within can use most of the visible length. This obviously makes the lower end of the damper fatter, but that in turn means it must reside farther forward (left in this view) to stay clear of the drive axle.
If this was a Toyota we’d see a slender rod in this area, with the shock’s working diameter ending above this point. That allows their shocks to hug closer to the axle, but such shocks must extend higher at the top to maintain sufficient suspension travel. This may explain why the Ram’s high-mount upper arm pivot (and the upper shock mount that’s usually part of that structure) isn’t positioned nearly as high as we’d see on a Toyota.
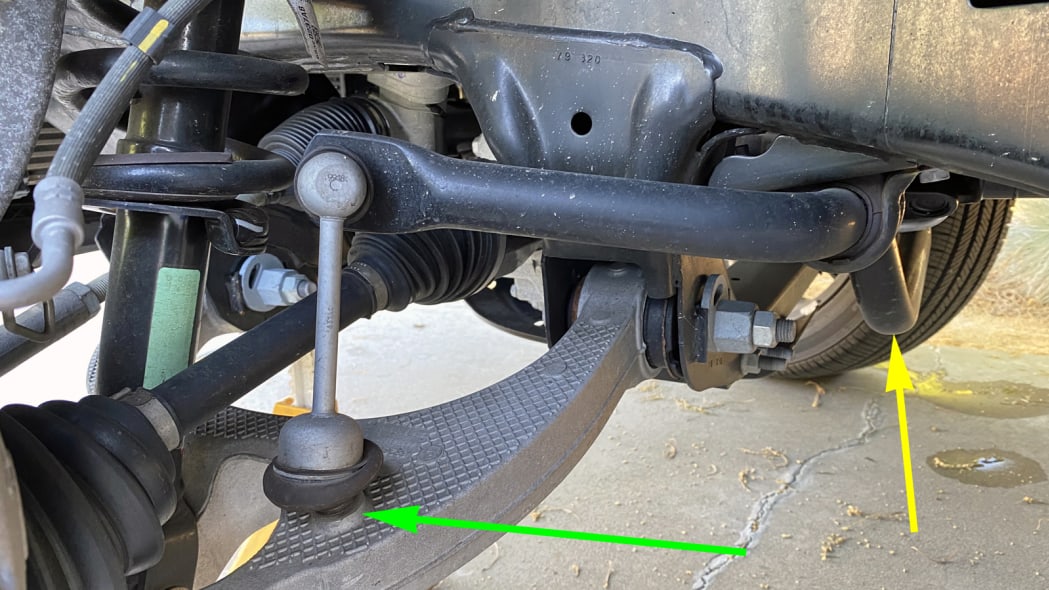
The 2019+ Ram 1500’s stabilizer bar (yellow) has been moved from its former position ahead of the axle to this position behind the axle. It’s a very tidy installation. They say it results in a 20% increase in roll stiffness, but the old installation seemed to have room enough for fatter bars that could offer that kind of gain.
I think the real reason for the increased roll stiffness has to do with the capacity of the linkage mounting point (green) on the lower wishbone. The old design’s mounting point was a flange that protruded away from the main wishbone casting. They were probably near the limit of what it could take. Whether that’s strictly the case or not, this design transmits the stabilizer bar load into the very meaty central part of the wishbone. I like how it mirrors and counterbalances what’s going on with the shock, too. All of this results in a tidier and lighter lower wishbone design.
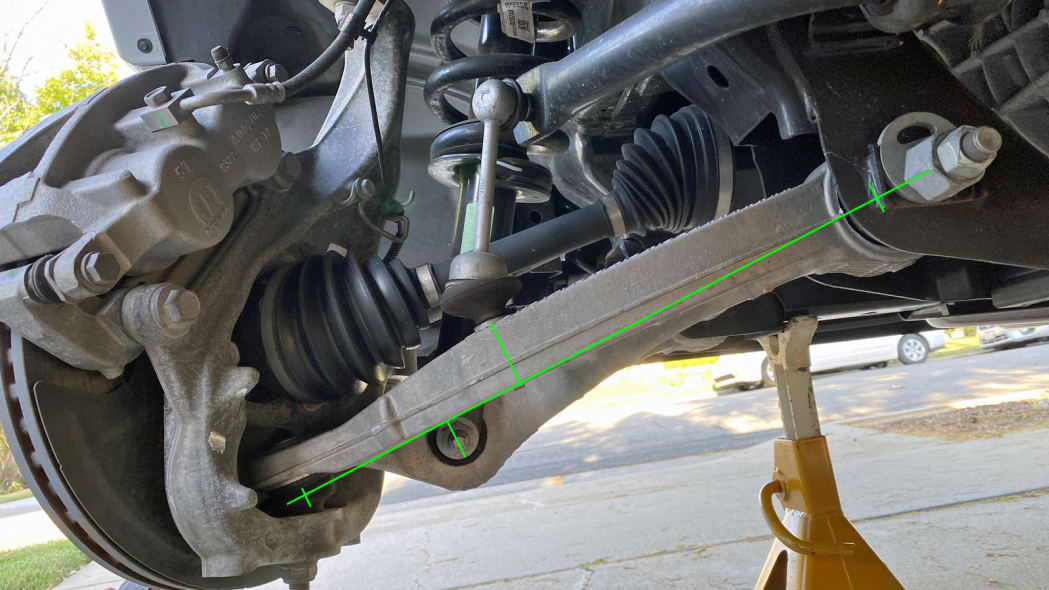
The distortion in photos like this always make estimating motion ratios a little dicey, but I’m going to plow ahead anyway. The point isn’t to reverse engineer this truck, just see what it's all about.
Looking first at the inner pivot at the frame and the outer ball joint at the steering knuckle, our spring shock assembly bolts to the arm about 75% of the way out. Every inch of suspension travel will result in 0.75 inch of spring and shock movement. The stabilizer bar link looks like it lines right up with that, but you’ve got to follow the mounting bolt down from the flexible joint hidden inside that rubber bellows. That reveals a motion ratio of about 60%, or 0.6 inch of stabilizer bar linkage movement for every inch of wheel travel.
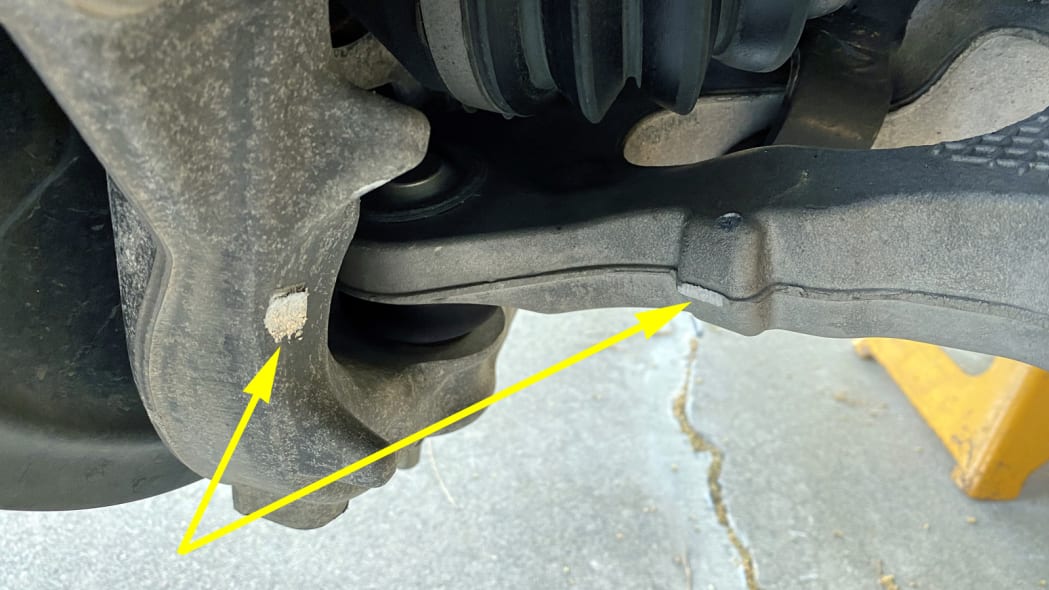
Many trucks have mechanical steering stops, and the Ram 1500 is no exception. The lower wishbone has a special protrusion that matches up to a zone built into the steering knuckle. This one comes into play at full left lock, while a similar setup on the passenger side does the job at full right lock. This doesn’t happen often, and there’s never pressure for extended periods, so it's fine. I prefer this to having the steering gear itself hit a hard internal limit.
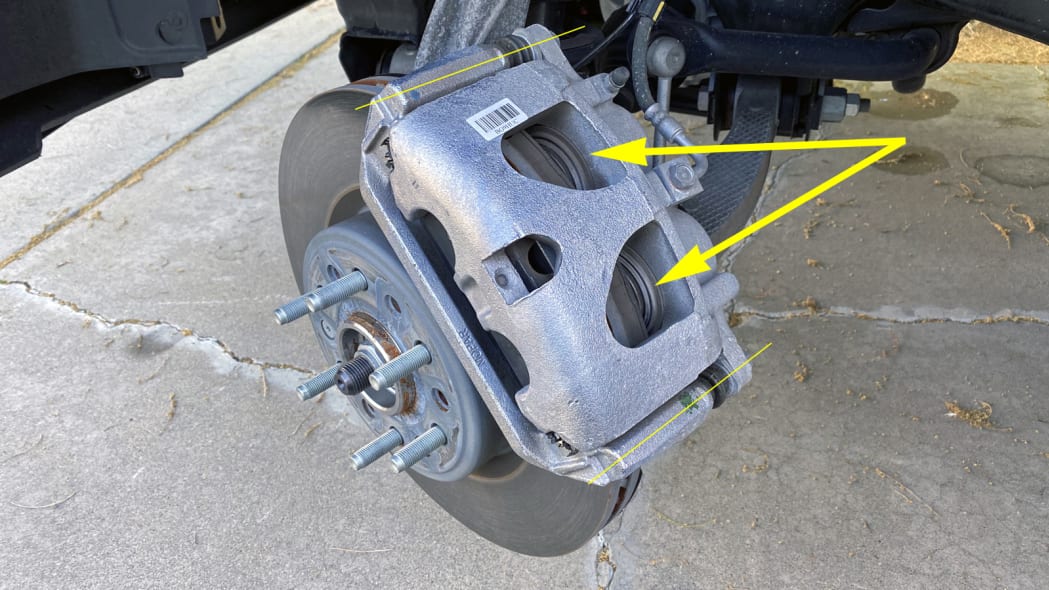
Normally we only see the bumps in the casting that give away a caliper’s pistons, but here we can see where this sliding caliper’s two pistons press against the inner brake pad. But it's not just the inner pad that does the work. The caliper itself slides (hence the name sliding caliper) on two pins as force is applied so that half of the clamping force generated by the inner pistons passes through the structure to the pads that are arrayed on the opposite side of the rotor.
It’s like grasping something between your fingertips and palm. Your fingers appear to be doing all of the work, but the item you’ve grabbed is experiencing the same clamping force on both sides.
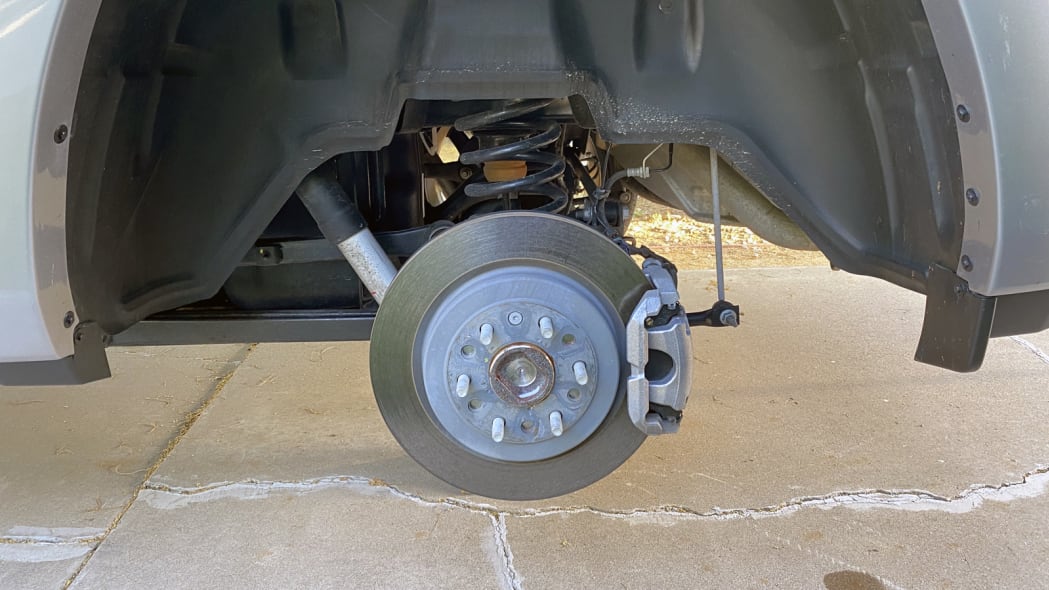
Just about everything we’re seeing at the back of the Ram 1500 is unique in the North American pickup world. The only truck that’s similar is the new Jeep Gladiator, which makes sense because that truck only exists because it had this truck to borrow from.
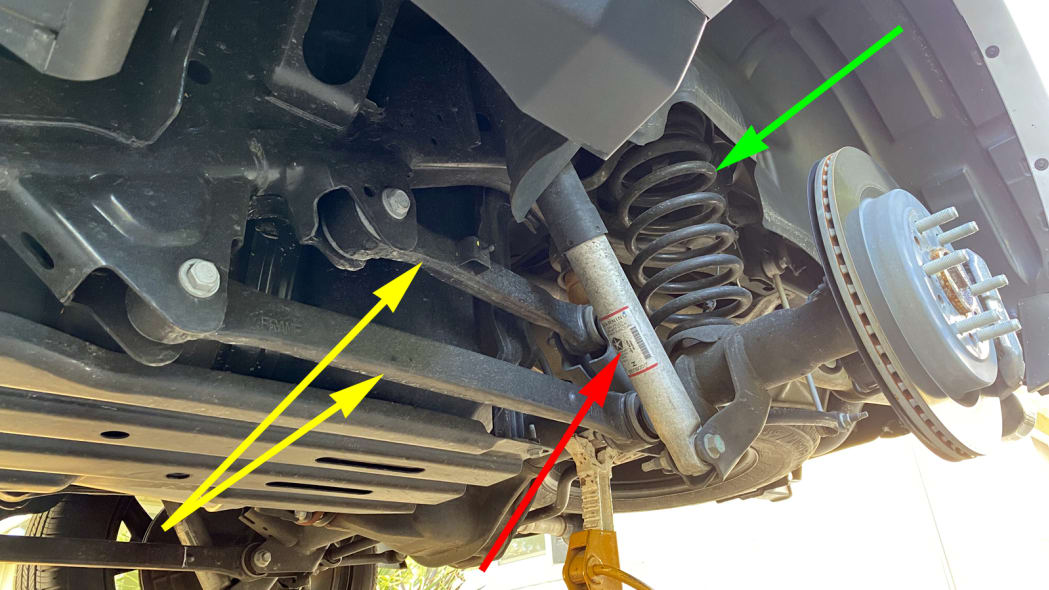
This rear suspension type may be unique among pickups, but this layout replaced leaf springs underneath frame-based SUVs more than three decades ago. People ride in the back of those, not bags of cement, so the ride and handling benefits were recognized as essential long ago. In fact, full-size SUVs have even moved on from there to the next level: independent rear suspension. And then there are all of those crossovers of all sizes.
Full-size trucks that tow and haul may not ever go that far, but this layout does make a lot of sense — especially since most trucks nowadays are sold with humongous crew cabs and shorter 5.5-foot beds.
Ram calls this link-coil suspension, but its other names include five-link rear suspension and four-link rear suspension. Those mean the same thing, with the difference coming down to a friendly disagreement on the status of the panhard bar, which both of them have.
Here we can see two trailing links (yellow), and you can imagine the two just like them on the other side. Atop the axle sits the all-important coil spring (green). The shock absorbers (red) can lean forward on both sides here because the four trailing links control axle windup. There’s no need for the staggered shock arrangement that leaf-spring trucks must use.
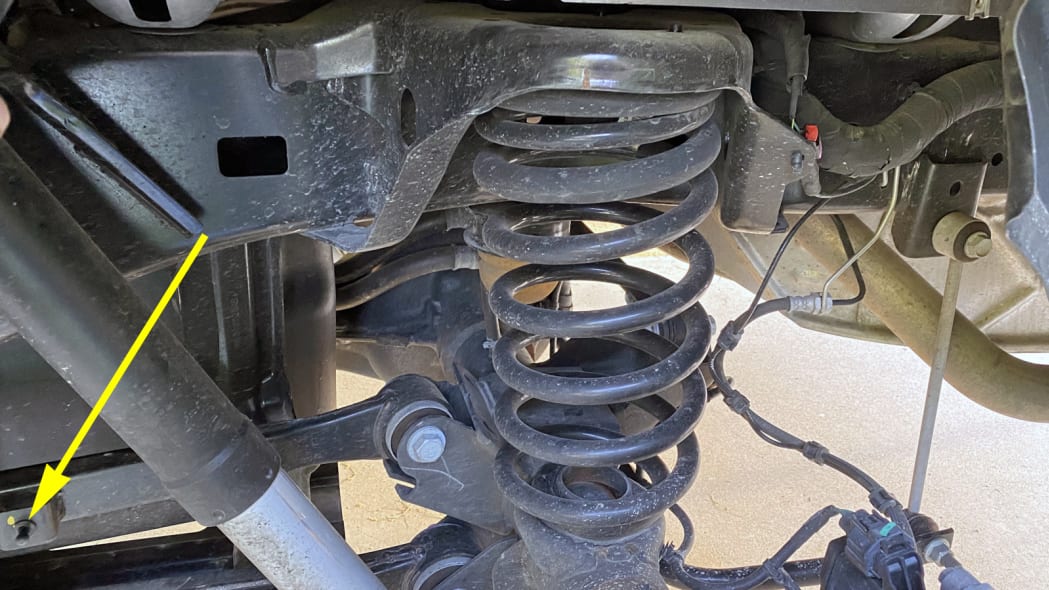
Unlike leaf springs, coil springs only have one job. They’re also better suited to that job because there are no sliding surfaces that come into play as they compress. The 2019+ Ram 1500 has progressive rear springs, which is why the coils appear closer together at the top. This allows the initial movement to be softer in the unladen condition, then tighten up as the suspension compresses over bigger bumps and when the truck is burdened with a load.
It’s easy to imagine how an air spring can be substituted very easily. Everything else pretty much stays the same. A height sensor would be connected to the nub (yellow) on the uppermost trailing link, and there would be a few valves and hoses that run off to an added air compressor.
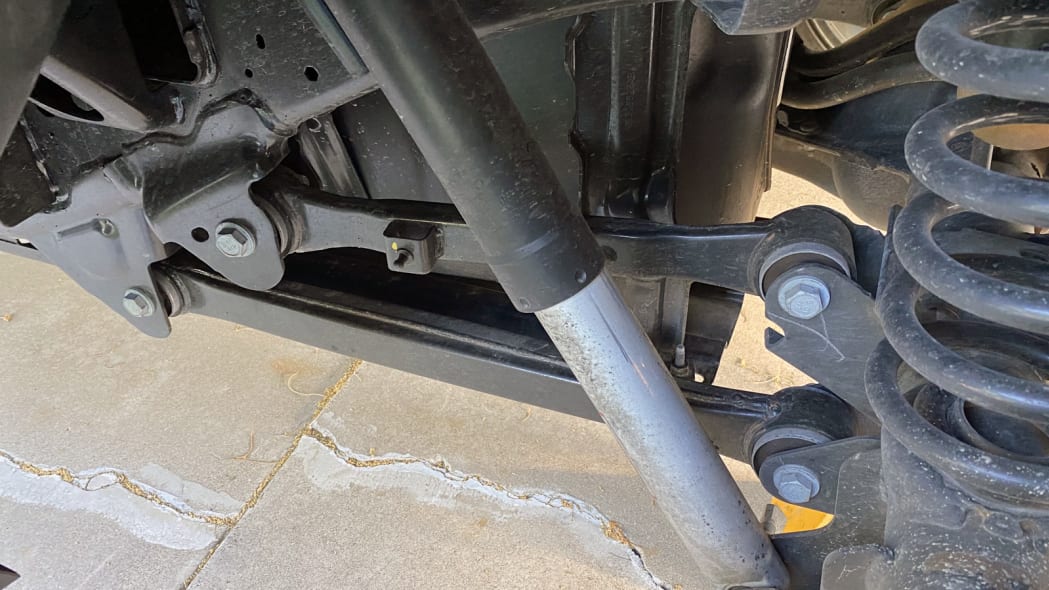
One of the many advantages of link-coil suspension is a reduction in weight. When it first came out in 2009 Ram claimed a 40-pound weight savings, with much of that being unsprung weight. Leaf springs are long, thick and heavy. These links are something like a third as long, and they’re hollow. As for the coil springs, they don’t weigh much.
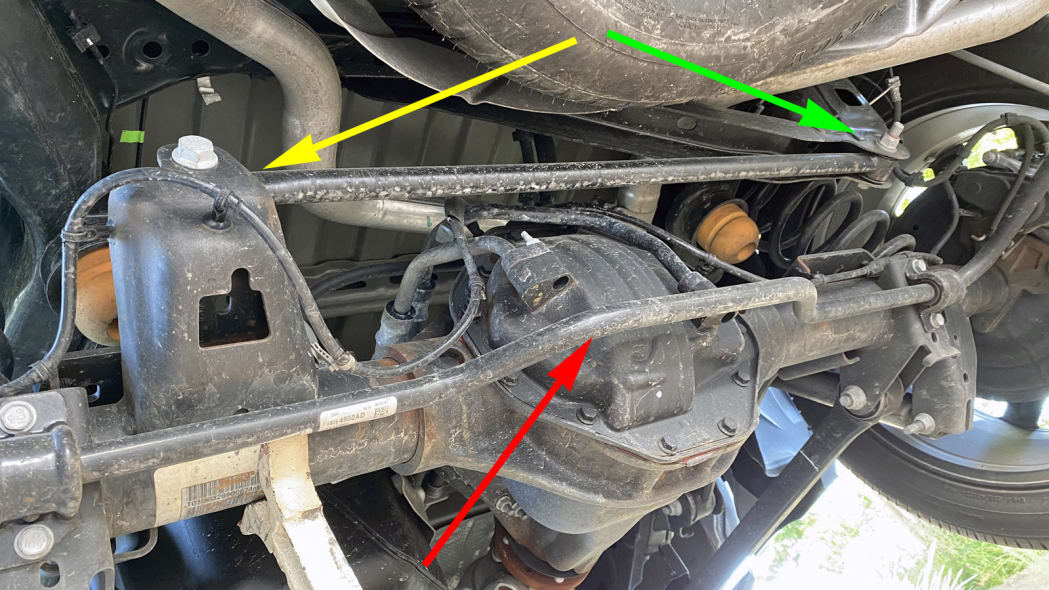
Here is link number five, the panhard bar. Some will call it a track bar. Pick your poison. This is the link that keeps the axle from moving side-to-side, and it is the very presence of this link that made me so impressed with the downhill, winding road towing stability offered by this layout. Leaf-sprung trucks don’t (and can’t) have one of these. They instead depend on the lateral stiffness of the pivot bushings that live way out at their ends. That plan isn’t near as reliable as this.
The left end bolts to bracketry (yellow) that’s part of the axle, while the right end attaches to brackets (green) that descend from a frame crossmember. The axle is well braced whether you’re cornering left or right. It is as long as it is to reduce the amount of left-right translation that will occur as the suspension moves up and down.
Meanwhile, just below is the stabilizer bar (red), a feature we almost never see on leaf-spring trucks because it becomes a packaging and assembly nightmare.
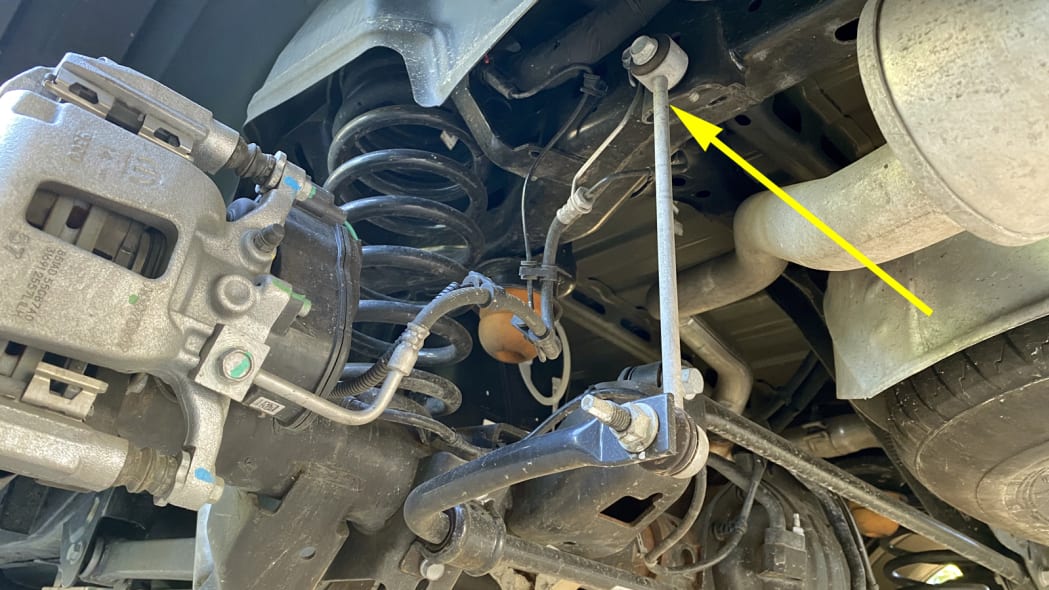
The rear stabilizer bar link (yellow) attaches to a bracket on the frame.
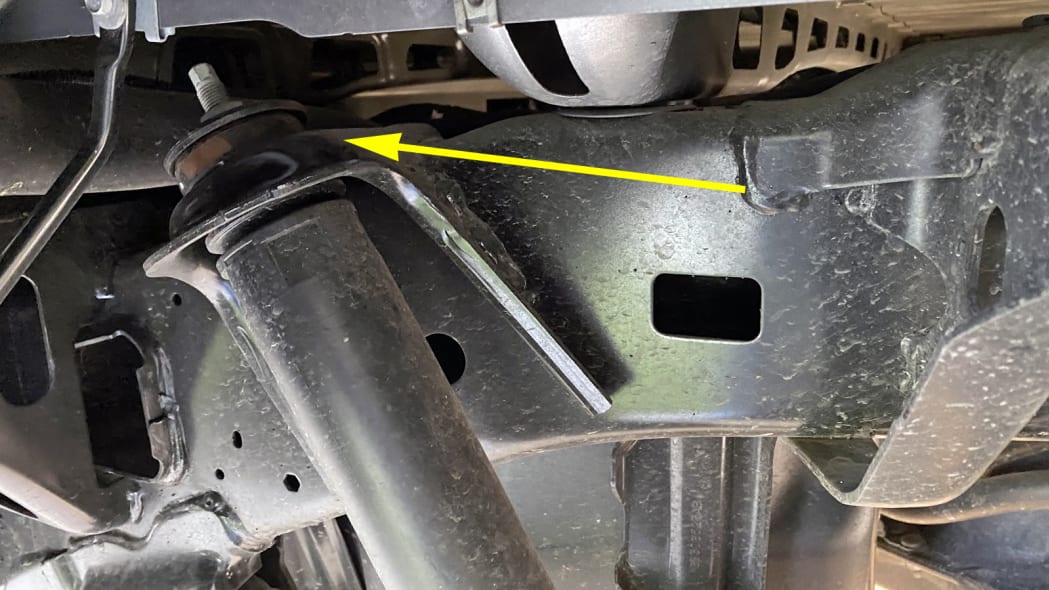
There’s nothing too special about the upper shock mounts (yellow) other than they’re fairly conventional and easy to get at if you ever want to make a change.
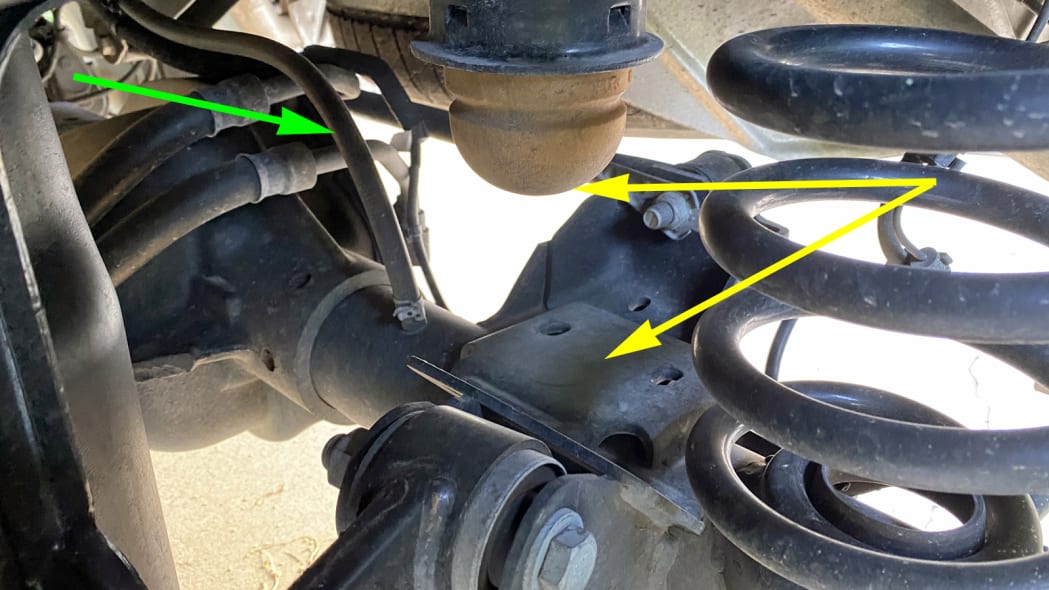
Urethane bump stops (yellow) are positioned adjacent to the coil springs. The availability of optional air suspension makes it impossible to position them within the coils. Meanwhile, the rear axle is equipped with a breather tube (green) to aid water crossings.
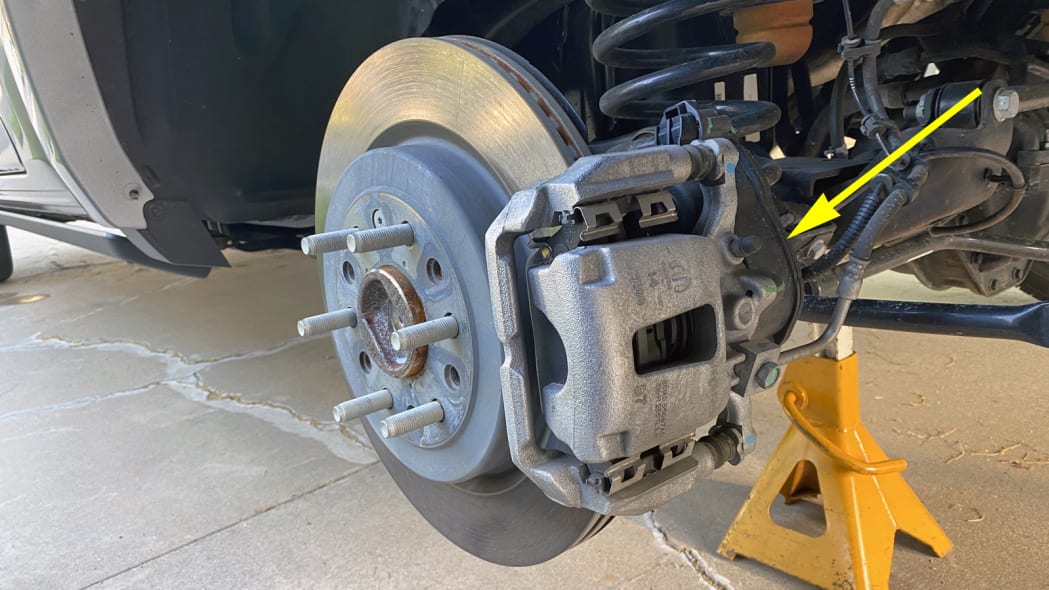
The rear brakes on this Laramie consist of single-piston sliding calipers, ventilated rotors and an electronically-applied parking brake (yellow) that is built into the calipers.
This Laramie test truck is equipped with optional Night Package and blacked-out 22-inch rims that are wrapped with 285/45R22 Goodyear Eagle Touring tires. I didn’t expect something with this much tire width and wheel diameter (and so little sidewall) to be light, and they’re not. How does 83.5 pounds grab you? They certainly look good, though.
I drove this 2020 Ram 1500 4x4 extensively again this week, and I’m still greatly impressed with the ride this truck produces despite these heavy optional rims. And we’re not even riding on air suspension at this point. The competition has a lot of catching up to do when it comes to creating a suspension that excels at everyday use. At least one competitor seems bent on chasing payload ratings for a marketing advantage, but I think this suspension is great at keeping things real. I, for one, hope that the others get it in gear quick. That said, I’m sure Ram will be happy as clams if they don’t.
Contributing writer Dan Edmunds is a veteran automotive engineer and journalist. He worked as a vehicle development engineer for Toyota and Hyundai with an emphasis on chassis tuning, and was the director of vehicle testing at Edmunds.com (no relation) for 14 years.
You can find all of his Suspension Deep Dives here on Autoblog.